Insect feeding – What does the system need to be capable of?
Not always as easy as it looks
Systems for dry and liquid feeding of insects must be tailored to the size of the insect fattening system; there should also be the option of expanding the system at a later date. Since high-precision rearing conditions and meticulous EU regulations must be adhered to, the system must also be able to implement them. Optimal quality and perfect hygiene are essential when using insects as a feedstuff.
Criteria
First of all, the question arises as to which insects should be fattened in which trail size, as different insects require different things of the technology. Below we outline some of the ideal conditions for breeding of:
Soldier fly larvae
- ambient temperature between 27 °C and 30 °C
- good ventilation (with > 1,000 larvae in a rearing box, temperatures of over 50 °C occur)
- food source – organic materials in compliance with feedstuff regulations
- constant availability of feed (conversion of up to 50% of feed into new body mass)
- absorbent feed and growth substrate (release of metabolic products and liquids)
Mealworms
- Ambient temperature between 20 °C and 23 °C, and high humidity
- thermophilic insect – activity depends on ambient temperature (heat death after four hours at 42 °C, development stops at 10 °C)
- good ventilation to prevent mould growth, mite infestation and heat build-up
- preferably dark and enclosed areas (dust!)
- multiple tanks for all 3 development stages
- food source: bran, grain – moist feed (change daily to avoid mould mite infestation)
- depending on the number of larvae and the size of the box, they need to be fed anywhere from once a day to once a week (larvae can survive up to nine months without food, cold-tolerant)
Installing a ventilation system for the entire husbandry area is advisable and, depending on the species, sometimes indispensable. It ensures a constant exchange of ambient air and supplies the animals with fresh air.
Sufficient distance between the tanks promotes the removal of the warm and moist air that is constantly produced during feeding, moulting and pupation. For industrial purposes, temperature and humidity control must be combined with air circulation throughout the entire husbandry area.
Process optimisation
In this context, process automation, as a cross-sectional technology in all process engineering industries, enables the design of economical, safe and environmentally friendly production. As such, automation provides an integrated overall solution that enables insect breeding within a production line. Only when every processing unit involved works in tandem can access be enabled to scale-up solutions – e.g. through parallel breeding or conveyor belts – to achieve a defined throughput rate and thus ensure the economic efficiency of the processing.
The system design is centred around minimising the need for manpower and optimising processes, as well as consistent and reliable processes that guarantee consistent quality.
High standard of hygiene required
The bigger the farm, the higher the risk of diseases being brought in and disrupting processes. All of the feeding technology must be designed to ensure perfect hygiene to prevent the introduction of disease, funghi and bacteria.
Early warning systems are already under development for future integration into the system technology.
Dispensing of minute quantities
Absolute precision of the feed dosing with no residues (spillages during dry or liquid dosing) is decisive. The addition of minimum quantities in liquid or dry form, e.g. of required additives, should also be taken into account.
It is very important to ensure that these additives are precisely measured: While an extra microgram of medicine would be of little consequence for a fully grown cow weighing 600 kilograms (except in terms of cost) it would prove fatal for a 0.5 gram mealworm. And adding additives to feed is important, because feeding fattening insects can come with various issues, such as mould growth, parasite infestation and disease. Precise measurement of water/moisture is also vital. Further requirements:
- easy system operation, as programmed by TEWE
- low costs
- powerful shredding, mixing and dosing technology
- interruption-free logistics from beginning to end with semi-automatic and fully automatic processes
- optimal hygiene at every stage
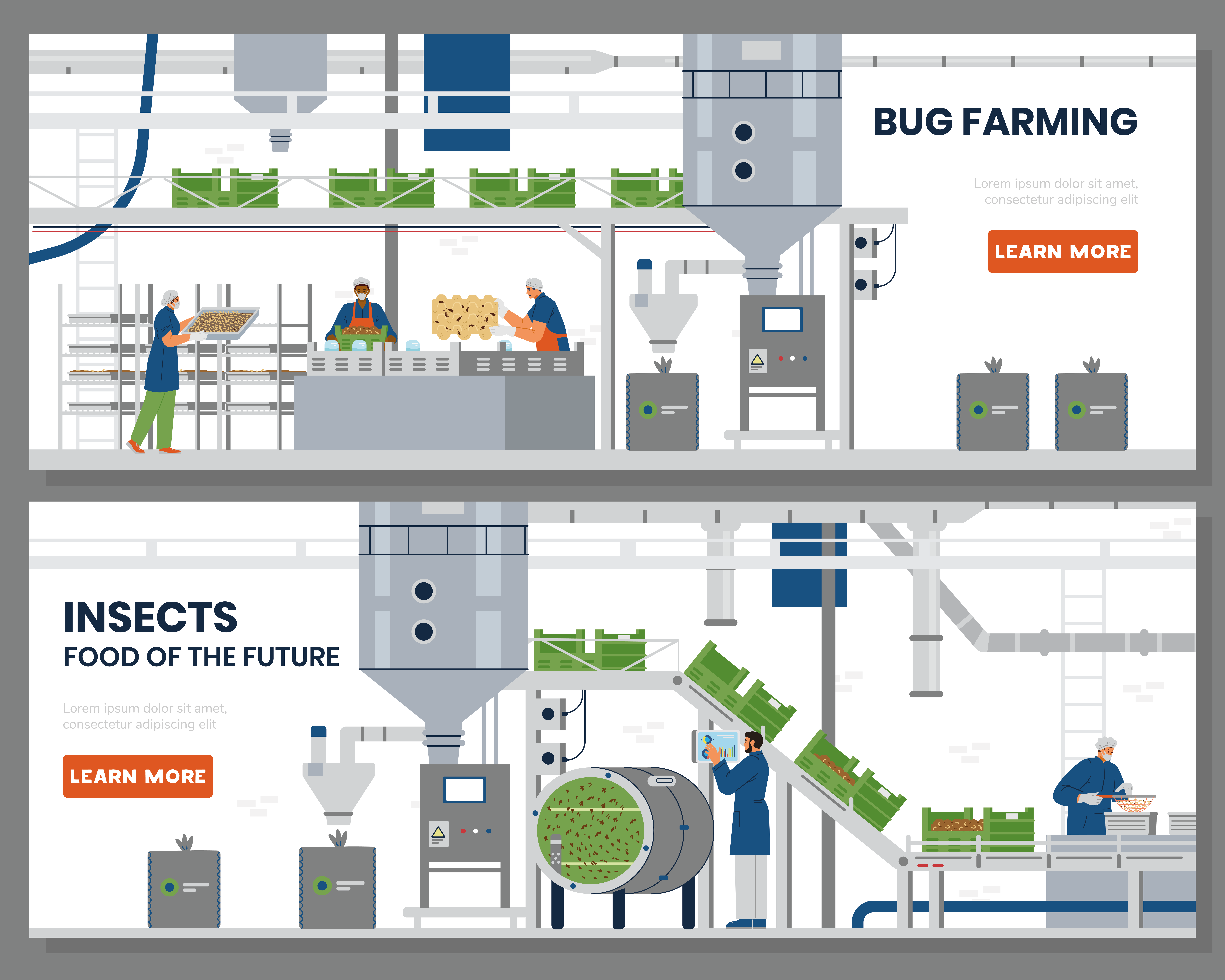
Minimum requirements
There many technical and hygienic minimum requirements that insect feeding systems have to meet to ensure success and compliance with EU standards. These are the key requirements:
- Technical requirements
- Precise dosing: Feeding systems must be able to dose the exact amount of feed required. This is vital in ensuring a consistent supply of feed to the insects.
- Automation: Fully or semi-automatic systems are preferred as they maximise efficiency and minimise human error.
- Homogeneous feed: Systems for thorough mixing of the feed batches (agitators and pump programs) are necessary to ensure an even distribution of nutrients.
- Adaptability: The systems need to be adaptable to small and large insect farms.
- Versatility: The ability to supply different feed types (liquid and dry) and nutrient compositions.
- Hygiene requirements
- Cleaning programs: Thorough automatic cleaning and rinsing programs are necessary to ensure a high standard of hygiene and prevent the spread of pathogens.
- Materials: It is vital to use materials which are easy to clean and disinfect, such as stainless steel.
- Prevention of contamination: Systems need to be designed to prevent contamination by dripping or spilt food.
- Process and data management
- Documentation: Extensive process documentation is essential to ensure traceability of and compliance with standards.
- Central control: Central control systems for all feeding processes and feed curves are key to maximising efficiency and precision.
- Data management: Efficient process and data management for the monitoring and optimisation of feeding processes.
- EU standards and regulations
- HACCP concept: Implementation of a HAACP (Hazard Analysis and Critical Control Points) concept ensures food safety.
- Regulations: Compliance with specific EU regulations for the breeding and use of insects as feed, such as Regulation (EU) 2017/893, which governs the use of insect proteins in aquaculture.
- Licences and certifications: Feeding systems and production sites must meet EU requirements regarding licences and certifications.
- Environment and sustainability
- Resource efficiency: The feeding systems must use resources efficiently to minimise the ecological footprint of insect breeding.
- Sustainable feedstuffs: Sustainable, locally sourced feedstuffs cause less environmental damage.
Referenzen
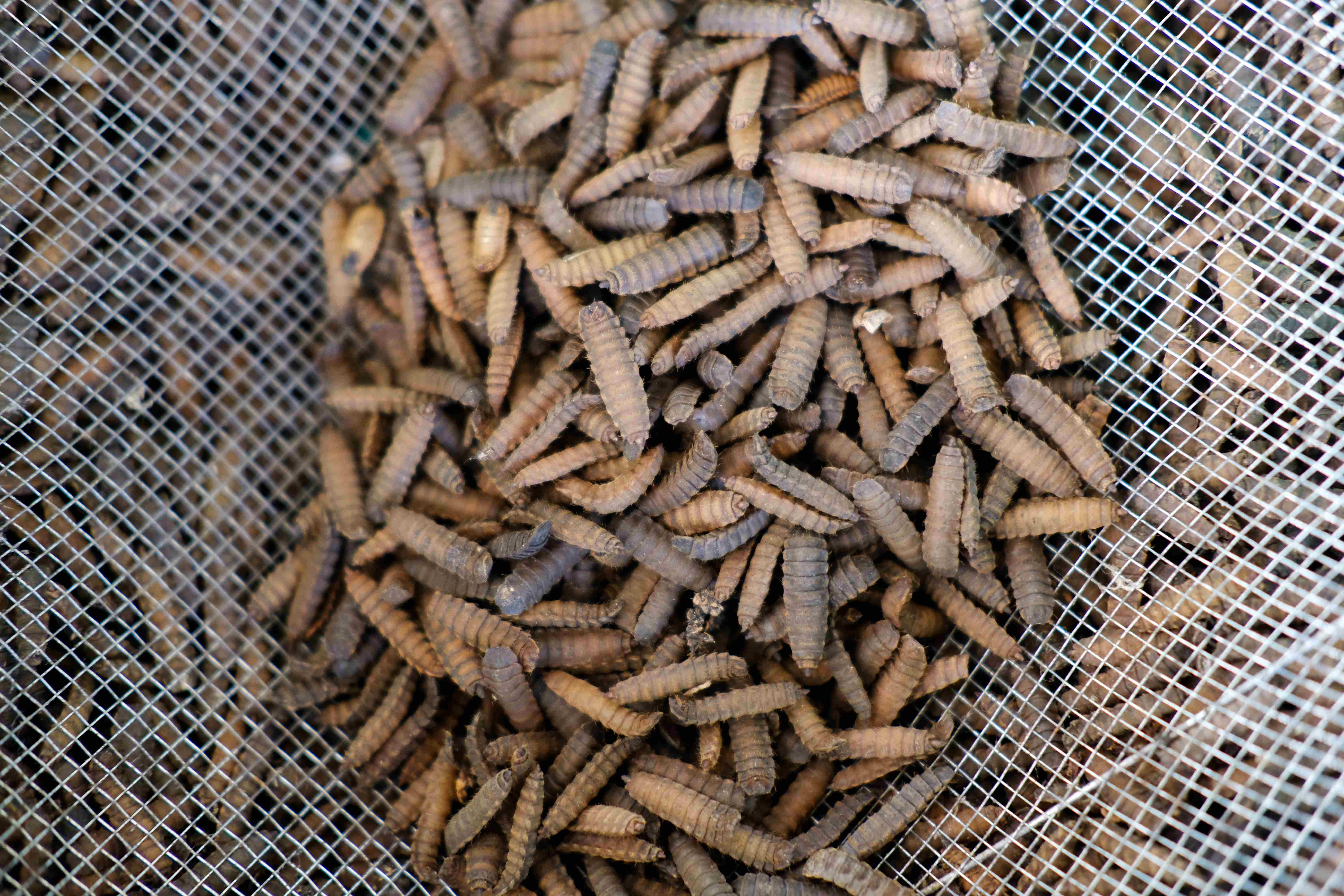
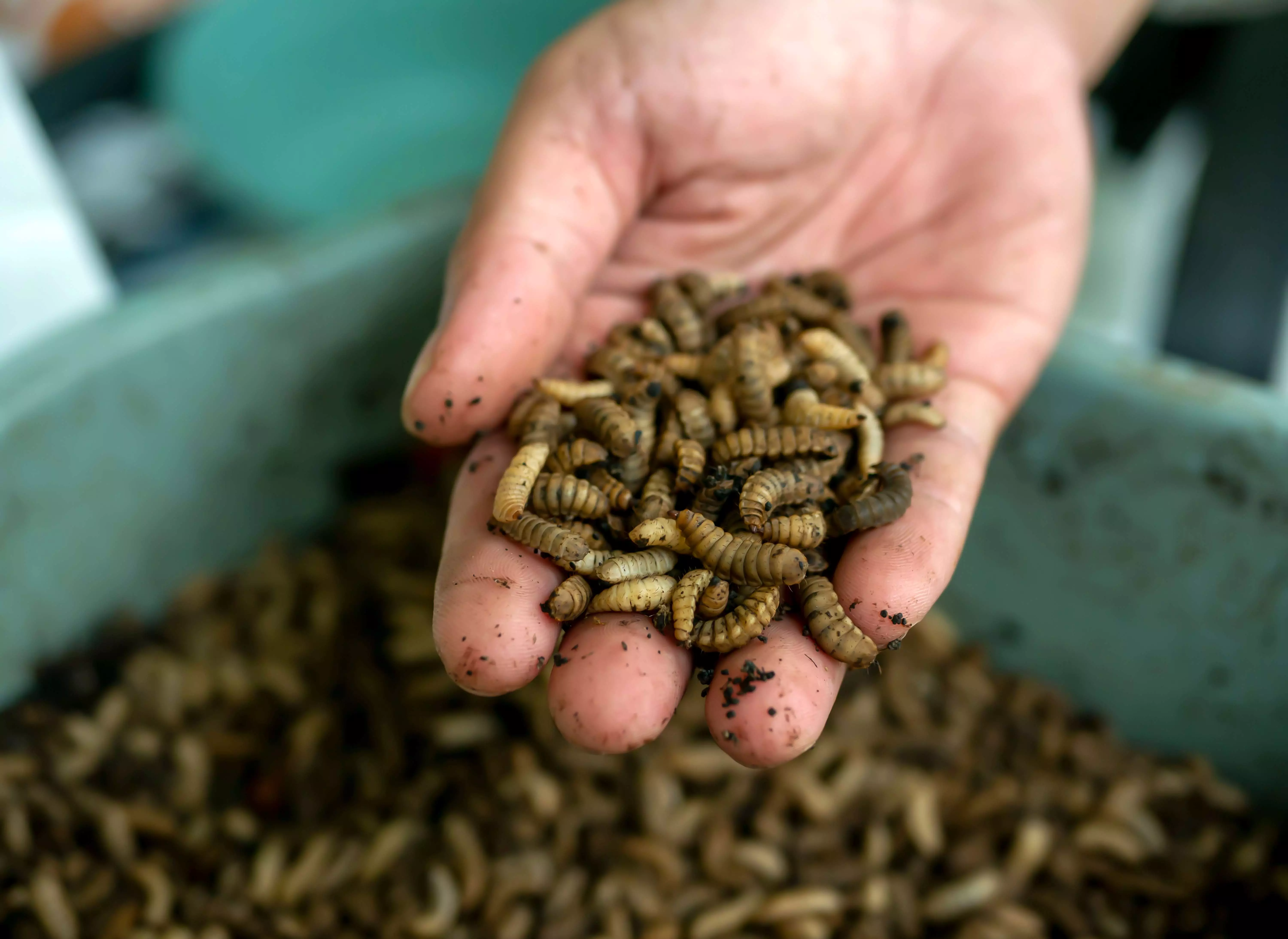
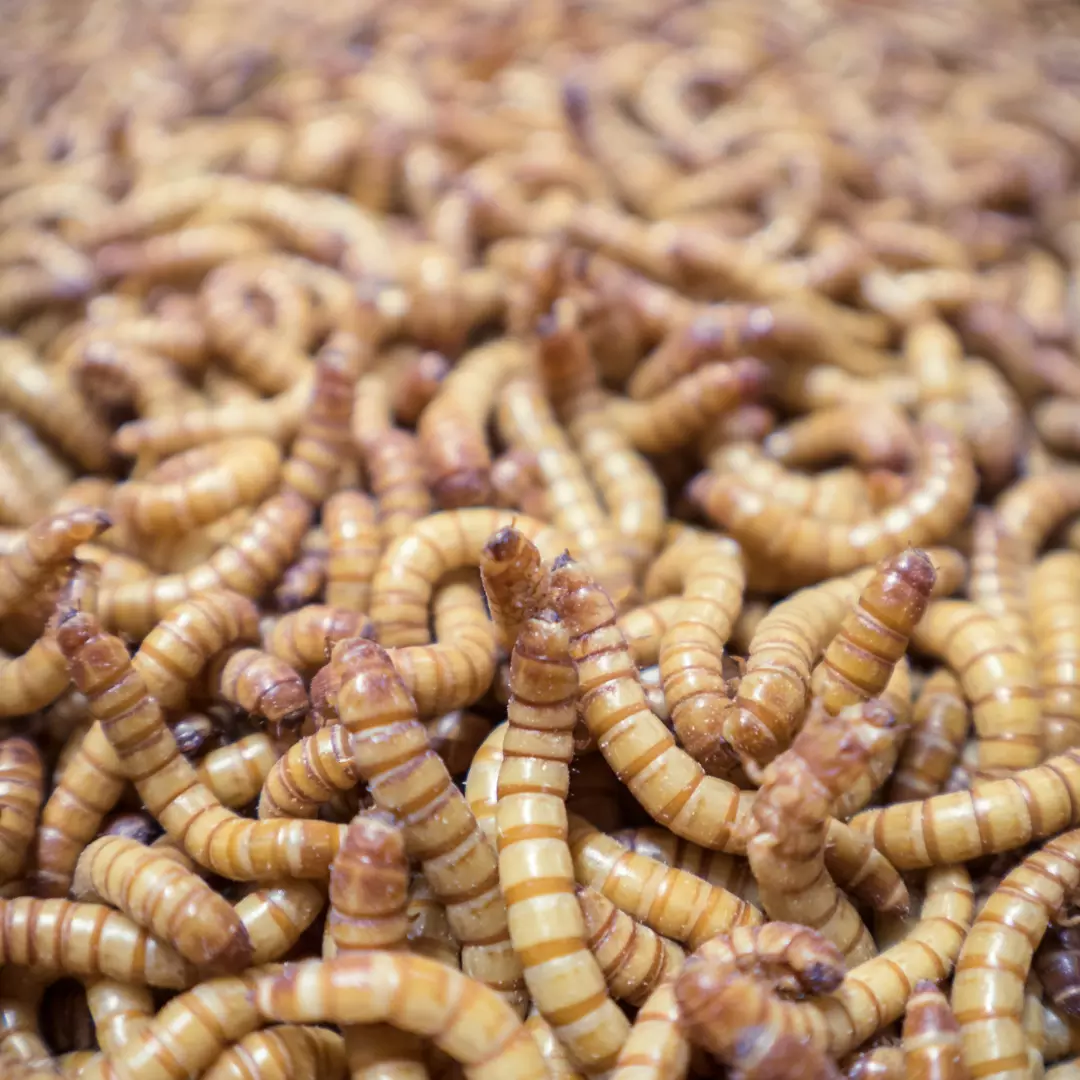